How to Make Activated Charcoal: A Comprehensive Guide
Editor’s Note: Given the importance of understanding the process of activated charcoal production, we have published this in-depth guide on “how to make activated charcoal”.
Our team has conducted extensive research and analysis to provide you with this comprehensive guide. We aim to equip you with the necessary knowledge to make informed decisions regarding activated charcoal production.
Key Differences: Activated Charcoal Production Methods
Method | Description |
---|---|
Physical Activation | Involves heating the source material in the presence of a gasifying agent, such as steam or carbon dioxide. |
Chemical Activation | Employs chemical agents, such as phosphoric acid or zinc chloride, to create pores in the source material. |
Main Article Topics
- Sourcing and Preparing the Raw Material
- Activation Process: Physical vs. Chemical
- Post-Activation Treatment: Washing and Drying
- Quality Control and Testing
- Applications and Benefits of Activated Charcoal
How to Make Activated Charcoal
Activated charcoal, a highly effective adsorbent, is widely used in various applications such as water purification, air purification, and medical treatments. Understanding the process of making activated charcoal is crucial for ensuring its quality and effectiveness.
- Raw Material: Selecting the appropriate starting material, such as wood, coconut shells, or coal.
- Carbonization: Heating the raw material in the absence of oxygen to create a porous structure.
- Activation: Treating the carbonized material with steam or chemicals to create a highly porous structure.
- Washing: Removing impurities and residual chemicals from the activated charcoal.
- Drying: Removing moisture from the activated charcoal to ensure its stability.
- Grinding: Reducing the activated charcoal to a desired particle size for specific applications.
- Quality Control: Testing the activated charcoal to ensure it meets the required specifications.
- Applications: Utilizing the activated charcoal for various purposes, such as water purification, gas adsorption, and medical treatments.
- Environmental Impact: Considering the environmental implications of activated charcoal production and disposal.
- Innovations: Exploring new methods and technologies for producing activated charcoal with enhanced properties.
These key aspects provide a comprehensive overview of the “how to make activated charcoal” process. Understanding these aspects is essential for manufacturers, researchers, and users of activated charcoal to optimize its production, applications, and environmental impact.
Raw Material
The selection of raw material is a critical step in the process of making activated charcoal, as it directly influences the final properties and performance of the activated charcoal.
The most common raw materials used for producing activated charcoal include:
- Wood: Hardwood species, such as oak and maple, are preferred due to their high carbon content and low ash content.
- Coconut shells: Coconut shells are a sustainable and renewable resource that produces activated charcoal with a high surface area and excellent adsorption capacity.
- Coal: Coal is a traditional raw material for activated charcoal production, but it can result in a higher ash content and lower surface area compared to wood or coconut shells.
The choice of raw material depends on the desired properties of the activated charcoal, such as surface area, pore size distribution, and chemical composition. For example, activated charcoal made from coconut shells is often preferred for applications requiring high adsorption capacity, while activated charcoal made from wood is suitable for applications where a high surface area is crucial.
Understanding the connection between raw material selection and the properties of activated charcoal is essential for manufacturers to optimize the production process and meet the specific requirements of various applications.
Raw Material | Advantages | Disadvantages |
---|---|---|
Wood | High carbon content, low ash content | Lower surface area compared to coconut shells |
Coconut shells | Sustainable, high surface area, excellent adsorption capacity | Higher cost compared to wood |
Coal | Traditional raw material, readily available | Higher ash content, lower surface area |
Carbonization
Carbonization is a crucial step in the “how to make activated charcoal” process, as it transforms the raw material into a porous structure with a high surface area. This porous structure is essential for the adsorption properties of activated charcoal, which make it effective in various applications such as water purification, air purification, and medical treatments.
During carbonization, the raw material is heated to a high temperature in the absence of oxygen. This process drives off volatile components and creates a porous structure within the material. The extent of carbonization, including the temperature and duration of heating, significantly influences the properties of the resulting activated charcoal.
For instance, a higher carbonization temperature generally leads to a higher surface area and increased adsorption capacity. However, it is important to optimize the carbonization conditions to achieve the desired balance of surface area, pore size distribution, and chemical composition for the intended application.
Carbonization Conditions | Effect on Activated Charcoal |
---|---|
Temperature | Higher temperature generally leads to higher surface area and adsorption capacity |
Duration | Longer duration can further increase surface area and pore development |
Atmosphere | Absence of oxygen is crucial for creating a porous structure |
Understanding the connection between carbonization and the properties of activated charcoal is essential for manufacturers to control the production process and tailor the activated charcoal to specific applications. By optimizing the carbonization conditions, manufacturers can produce activated charcoal with the desired surface area, pore size distribution, and chemical composition, ensuring its effectiveness for various adsorption applications.
Activation
In the process of “how to make activated charcoal”, activation is a crucial step that transforms the carbonized material into a highly porous structure with a large surface area. This enhanced porosity is what gives activated charcoal its exceptional adsorption properties, making it effective for various applications such as water purification, air purification, and medical treatments.
-
Physical Activation:
In physical activation, the carbonized material is heated in the presence of a gasifying agent, such as steam or carbon dioxide. This process creates a porous structure by removing portions of the carbon matrix, resulting in a high surface area.
-
Chemical Activation:
Chemical activation involves treating the carbonized material with chemical agents, such as phosphoric acid or zinc chloride. These chemicals react with the carbon, creating a porous structure with a high surface area and tailored surface chemistry.
-
Optimization of Activation:
The activation process can be optimized by controlling various parameters, such as temperature, duration, and the type of activating agent. Optimizing these parameters allows manufacturers to tailor the activated charcoal’s properties, such as surface area, pore size distribution, and surface chemistry, to meet specific application requirements.
-
Impact on Applications:
The properties of activated charcoal obtained through different activation methods and optimization impact its performance in various applications. For example, activated charcoal with a high surface area and tailored pore size distribution is preferred for applications requiring high adsorption capacity, while activated charcoal with specific surface chemistry is suitable for applications involving selective adsorption or catalysis.
By understanding the connection between activation and the properties of activated charcoal, manufacturers can optimize the activation process to produce activated charcoal with the desired characteristics for specific applications, ensuring its effectiveness in various fields.
Washing
In the process of “how to make activated charcoal”, washing is a crucial step that ensures the removal of impurities and residual chemicals from the activated charcoal. This step is critical for producing high-quality activated charcoal that meets the required standards for various applications, such as water purification, air purification, and medical treatments.
After the activation process, the activated charcoal may contain impurities and residual chemicals from the raw material or the activating agents used. Washing removes these impurities and residual chemicals by rinsing the activated charcoal with water or a suitable solvent. This process helps to enhance the purity and effectiveness of the activated charcoal.
The washing process can be optimized by controlling various parameters, such as the type of washing solution, temperature, and duration. Optimizing these parameters ensures the effective removal of impurities while preserving the desired properties of the activated charcoal.
Washing Parameter | Effect on Activated Charcoal |
---|---|
Type of washing solution | Determines the effectiveness of impurity removal |
Temperature | Higher temperature can enhance impurity removal |
Duration | Longer duration ensures thorough washing |
Understanding the connection between washing and the properties of activated charcoal is essential for manufacturers to optimize the washing process and produce activated charcoal with the desired purity and effectiveness for specific applications.
Drying
In the process of “how to make activated charcoal”, drying is a critical step that ensures the removal of moisture from the activated charcoal, enhancing its stability and performance. Moisture can adversely affect the activated charcoal’s adsorption capacity, making it crucial to control the moisture content to optimize its effectiveness in various applications.
-
Enhanced Adsorption Capacity
Drying activated charcoal removes moisture that can occupy its pores, hindering its adsorption capacity. Effective drying ensures that the activated charcoal’s pores are available for adsorption, maximizing its efficiency in removing impurities and contaminants from liquids and gases.
-
Improved Stability
Moisture can promote the growth of bacteria and other microorganisms on activated charcoal, affecting its stability and performance. Drying helps to prevent microbial growth, ensuring the activated charcoal’s stability during storage and transportation.
-
Prevention of Caking and Lumping
Moisture can cause activated charcoal particles to stick together, forming clumps or cakes. Drying helps to prevent caking and lumping, maintaining the activated charcoal’s flowability and ease of handling.
-
Extended Shelf Life
Properly dried activated charcoal has an extended shelf life compared to moist activated charcoal. Drying helps to preserve its adsorption capacity and stability over time, ensuring its effectiveness for extended periods.
Understanding the connection between drying and the properties of activated charcoal is essential for manufacturers to optimize the drying process and produce activated charcoal with the desired stability and performance for specific applications.
Grinding
In the process of “how to make activated charcoal”, grinding is a crucial step that reduces the activated charcoal to a desired particle size, enhancing its performance and suitability for specific applications. The particle size of activated charcoal significantly influences its adsorption capacity, reactivity, and flowability, making grinding an essential aspect of tailoring activated charcoal for various uses.
For instance, in water purification applications, a smaller particle size of activated charcoal provides a larger surface area for adsorption, resulting in enhanced removal of impurities and contaminants. Conversely, a larger particle size may be preferred for air purification applications, where it offers reduced pressure drop and better flow dynamics within the filtration system.
Grinding also affects the reactivity of activated charcoal. Smaller particles have a higher surface area-to-volume ratio, leading to increased active sites for chemical reactions. This enhanced reactivity is beneficial in applications such as catalysis and electrode materials.
Particle Size | Effect on Activated Charcoal |
---|---|
Smaller Particle Size | Increased adsorption capacity, enhanced reactivity |
Larger Particle Size | Reduced pressure drop, better flow dynamics |
Understanding the connection between grinding and the properties of activated charcoal is essential for manufacturers to optimize the grinding process and produce activated charcoal with the desired particle size distribution for specific applications. This ensures the effective performance of activated charcoal in various fields, including water purification, air purification, and chemical processing.
Quality Control
In the process of “how to make activated charcoal”, quality control is paramount to ensure the final product meets the desired specifications and performs effectively in its intended applications. Testing the activated charcoal involves a series of analyses to evaluate its physical and chemical properties, ensuring compliance with industry standards and customer requirements.
Quality control testing includes:
- Surface Area Analysis: Measuring the surface area of activated charcoal is crucial as it directly influences its adsorption capacity. A higher surface area provides more sites for adsorption, resulting in enhanced removal of impurities.
- Pore Size Distribution Analysis: Determining the pore size distribution is essential as it affects the types of molecules that can be adsorbed. Different applications require specific pore sizes to effectively target and remove contaminants.
- Chemical Composition Analysis: Identifying the chemical composition of activated charcoal ensures its suitability for various applications. The presence of certain elements or compounds can impact its adsorption properties and reactivity.
- Adsorption Capacity Testing: Evaluating the adsorption capacity of activated charcoal is critical to assess its effectiveness in removing specific contaminants. Standard tests are conducted to determine the amount of impurities that can be adsorbed per unit mass of activated charcoal.
Understanding the connection between quality control and “how to make activated charcoal” is essential for manufacturers to produce high-quality activated charcoal that meets the required specifications. Effective quality control ensures consistent performance, regulatory compliance, and customer satisfaction.
By implementing robust quality control measures, manufacturers can optimize the production process, minimize defects, and deliver activated charcoal that meets the desired standards for various applications, including water purification, air purification, and medical treatments.
Applications
Understanding the applications of activated charcoal is a crucial aspect of “how to make activated charcoal” as it drives the design, production, and optimization of this valuable material. The diverse applications of activated charcoal stem from its exceptional adsorption properties, making it a versatile tool in various industries and fields.
Let’s explore the connection between applications and the manufacturing process of activated charcoal:
- Water Purification: Activated charcoal is widely used in water purification systems to remove contaminants, impurities, and odors. Its high surface area and porous structure allow it to effectively adsorb organic compounds, chlorine, and other undesirable substances, resulting in cleaner and safer drinking water.
- Gas Adsorption: Activated charcoal plays a vital role in gas adsorption applications, such as air purification and odor control. It can effectively remove pollutants, toxins, and unpleasant odors from the air, creating a healthier and more comfortable environment. In industrial settings, activated charcoal is used to capture and recover valuable gases during manufacturing processes.
- Medical Treatments: Activated charcoal has medicinal properties and is used in various medical treatments. It can be administered orally to treat poisoning by adsorbing toxins and preventing their absorption into the bloodstream. Activated charcoal is also used in wound dressings to promote healing and prevent infection.
The diverse applications of activated charcoal highlight its versatility and importance in various sectors. By understanding the specific requirements of each application, manufacturers can tailor the production process to create activated charcoal with the desired properties, ensuring optimal performance and effectiveness.
Furthermore, ongoing research and development in activated charcoal applications continue to expand its potential. Exploring novel applications and optimizing existing ones drive innovation in the field of activated charcoal production, leading to advancements in water purification, air quality management, and healthcare.
Environmental Impact
The manufacturing and disposal of activated charcoal have environmental implications that must be considered in the context of “how to make activated charcoal.” Understanding these impacts helps us develop sustainable practices throughout the activated charcoal lifecycle.
-
Raw Material Sourcing
The sourcing of raw materials, such as wood or coconut shells, can impact deforestation and sustainable forestry practices. Responsible sourcing and the use of renewable resources are crucial to minimize environmental damage.
-
Energy Consumption
The production of activated charcoal involves high-temperature processes that consume significant energy. Employing energy-efficient technologies and utilizing renewable energy sources can reduce the carbon footprint of activated charcoal manufacturing.
-
Wastewater Generation
The washing and activation stages of activated charcoal production generate wastewater containing impurities and chemicals. Proper wastewater treatment and disposal are essential to prevent water pollution.
-
Greenhouse Gas Emissions
The carbonization process releases greenhouse gases into the atmosphere. Optimizing production techniques and employing carbon capture technologies can mitigate these emissions and promote a greener manufacturing process.
By considering the environmental impact and implementing sustainable practices, manufacturers can minimize the ecological footprint of activated charcoal production and disposal. This approach aligns with the principles of circular economy and responsible resource management.
Innovations
The pursuit of innovation is an integral aspect of “how to make activated charcoal.” By exploring new methods and technologies, manufacturers can produce activated charcoal with enhanced properties, expanding its applications and improving its performance.
-
Advanced Activation Techniques
Novel activation techniques, such as microwave or ultrasonic activation, offer precise control over the development of porosity and surface chemistry in activated charcoal. These methods can create activated charcoal with tailored properties for specific applications, such as enhanced adsorption capacity or selectivity.
-
Sustainable Raw Materials
The use of sustainable raw materials, such as agricultural waste or biomass, reduces the environmental impact of activated charcoal production. These alternative materials can be processed using innovative technologies to produce high-quality activated charcoal while promoting circular economy practices.
-
Novel Carbonization Methods
Exploring new carbonization methods, such as hydrothermal carbonization or electrochemical carbonization, allows for the production of activated charcoal with unique properties. These methods offer greater control over the carbonization process, leading to activated charcoal with enhanced surface area, pore structure, and adsorption capacity.
-
Functionalization and Modification
Post-production functionalization and modification techniques can enhance the properties of activated charcoal for specific applications. Chemical treatments or physical modifications can introduce functional groups or alter the surface chemistry of activated charcoal, improving its adsorption capacity for targeted contaminants or enhancing its stability and durability.
By continuing to innovate and explore new methods and technologies, manufacturers can develop activated charcoal with improved performance, sustainability, and versatility. These innovations contribute to advancements in water purification, air pollution control, and various industrial applications, ultimately leading to a more sustainable and efficient utilization of activated charcoal.
FAQs on Activated Charcoal Production
This section addresses frequently asked questions (FAQs) regarding the process of activated charcoal production, providing informative answers to enhance understanding.
Question 1: What is the primary raw material used in activated charcoal production?
Answer: The most common raw materials for activated charcoal production include wood, coconut shells, and coal. The choice of raw material depends on factors such as desired surface area, pore size distribution, and chemical composition.
Question 2: What is the purpose of the activation process in activated charcoal production?
Answer: Activation is a crucial step that creates a porous structure with a high surface area. This porous structure enhances the adsorption capacity of activated charcoal, making it effective for various applications such as water purification and air purification.
Question 3: What are the different activation methods used in activated charcoal production?
Answer: The two main activation methods are physical activation and chemical activation. Physical activation involves heating the carbonized material in the presence of a gasifying agent, while chemical activation uses chemical agents to create the porous structure.
Question 4: How does the washing process contribute to activated charcoal production?
Answer: Washing removes impurities and residual chemicals from the activated charcoal, ensuring its purity and effectiveness. Proper washing enhances the adsorption capacity and stability of activated charcoal.
Question 5: What are the key factors that influence the quality of activated charcoal?
Answer: The quality of activated charcoal is determined by factors such as surface area, pore size distribution, chemical composition, and adsorption capacity. Quality control measures are crucial to ensure that the final product meets the desired specifications.
Question 6: What are the potential environmental impacts associated with activated charcoal production?
Answer: Activated charcoal production can have environmental implications, including raw material sourcing, energy consumption, wastewater generation, and greenhouse gas emissions. Sustainable practices and responsible waste management are essential to minimize these impacts.
These FAQs provide a comprehensive overview of the key aspects and considerations involved in activated charcoal production. Understanding these aspects enables informed decision-making and optimization of the production process.
Transition to the next article section: Applications of Activated Charcoal
Tips on Activated Charcoal Production
Mastering the art of “how to make activated charcoal” involves careful considerations and techniques. Here are some valuable tips to guide you:
Tip 1: Selecting the Optimal Raw Material
The choice of raw material significantly influences the properties of activated charcoal. Wood, coconut shells, and coal are commonly used, each offering unique advantages. Consider factors such as surface area, pore size distribution, and chemical composition when selecting the raw material.
Tip 2: Optimizing the Carbonization Process
Carbonization is crucial for creating the porous structure of activated charcoal. Temperature, duration, and the absence of oxygen are key parameters to control. Higher temperatures generally lead to higher surface areas, but careful optimization is essential to achieve the desired properties.
Tip 3: Choosing the Appropriate Activation Method
Physical activation using steam or carbon dioxide, and chemical activation using chemicals like phosphoric acid, are the two main activation methods. The choice depends on the desired surface chemistry and pore structure. Experimentation and analysis are recommended to determine the optimal activation method.
Tip 4: Ensuring Thorough Washing
Washing is essential to remove impurities and residual chemicals from activated charcoal. Use appropriate washing solutions and optimize parameters like temperature and duration to ensure effective removal of contaminants. Proper washing enhances the purity and adsorption capacity of activated charcoal.
Tip 5: Achieving the Desired Particle Size
The particle size of activated charcoal affects its performance in various applications. Grinding techniques can be employed to achieve the desired particle size distribution. Smaller particles offer higher surface area, while larger particles may be preferred for applications requiring lower pressure drop.
Tip 6: Implementing Quality Control Measures
Rigorous quality control is paramount to ensure the consistency and effectiveness of activated charcoal. Establish clear specifications for surface area, pore size distribution, chemical composition, and adsorption capacity. Regular testing and analysis are crucial to maintain product quality.
Tip 7: Considering Environmental Impact
Activated charcoal production has environmental implications. Sustainable sourcing of raw materials, energy-efficient processes, and proper waste management are essential. Explore innovative technologies and best practices to minimize the environmental footprint of activated charcoal production.
Tip 8: Exploring New Innovations
Ongoing research and development lead to advancements in activated charcoal production. Stay updated with emerging technologies, such as microwave activation and novel carbonization methods. Exploring new innovations can enhance the properties and applications of activated charcoal.
By incorporating these tips into your activated charcoal production process, you can optimize the quality, performance, and sustainability of your products. Remember, continuous learning, experimentation, and attention to detail are key to mastering the art of “how to make activated charcoal”.
Conclusion
This comprehensive exploration of “how to make activated charcoal” has illuminated the intricacies of its production process and highlighted its remarkable properties. Activated charcoal’s exceptional adsorption capacity, versatility, and environmental impact make it an indispensable material in various industries.
Understanding the key steps involved in its production, from raw material selection to activation and quality control, empowers manufacturers and users alike to optimize its effectiveness. By embracing sustainable practices and exploring new innovations, we can harness the full potential of activated charcoal for a cleaner, healthier, and more sustainable future.
Youtube Video:
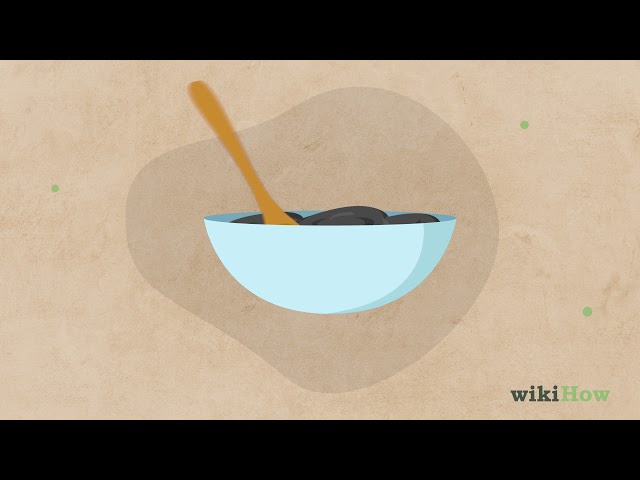